Whether you need a refresher on stock rotation or are learning about it for the first time, you’ve come to the right place. Stock rotation isn’t glamorous, but it’s important and can save a business thousands of dollars.
What Is Stock Rotation?
Stock rotation is the process of organizing inventory to mitigate stock loss caused by expiration or obsolescence. Basic stock rotation entails moving products with impending sell-by dates to the front of the shelf and moving products with later expiration dates to the back.
FUN FACT: Infamous mobster Al Capone’s brother, Ralph Capone, has been credited with inventing expiration date labels for milk back in the 1930’s.
Depending on the size of the store, the job of stock rotation can fall on anyone from inventory managers and hired stock associates to managers and sales associates. Brand reps should also always check their product when they make site visits and rotate any stock if need be. Stock loss is part of working with perishable goods, but if it happens too often, it could be because of poor stock rotation or improper ordering.
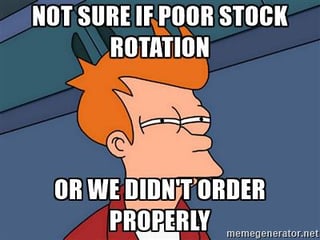
If you’re a retailer, your stock rotation policies are a very important component to how you stock your shelves, organize your store, and reduce losses. If you’re a merchandiser or brand, you need to know the standard policies of your retailers and educate them on the stock rotation policy that best fits your product(s).
The Methods
FIFO
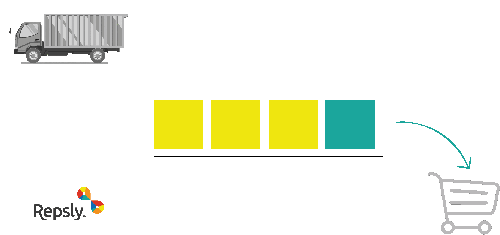
First in, first out (FIFO) is the the preferred method of stock control for most retailers, especially in the food and beverage space. When new stock comes in, it gets put in the back, pushing the older stock forward to be sold first. While this may seem like a no-brainer and saves retailers thousands of dollars in lost product, not every store takes the time to do it.
FEFO
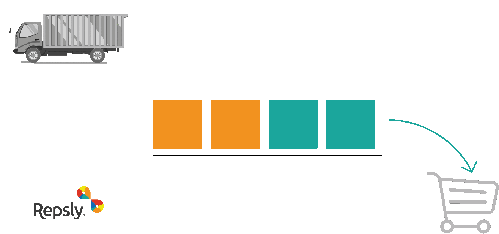
First expired, first out (FEFO) takes into account that what retailers receive from the warehouse may not necessarily be the freshest product. Instead of defaulting to putting the newest incoming stock in the back, the expiration dates are checked. The freshest product goes in back and the oldest product goes in front. This technique takes more time to execute, but is worth it for perishable products with short-term shelf lives. If any accidental mixing has occurred, either by an associate or a customer, FEFO also helps catch it.
LIFO
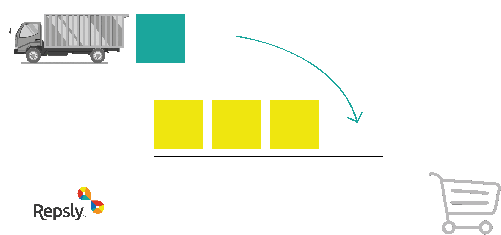
Last in, first out (LIFO) is not used as commonly in stores, but is still worth noting. LIFO is more often used with heavier, fast-moving, non-perishable or homogeneous goods in warehouses, when rotating items is not essential, practical or time-efficient.
The benefits of LIFO are mostly associated with accounting because retailers end up matching the most recent cost against their revenue. If your costs are rising, this process makes for more accurate forecasting than using older pricing, and better forecasting = better reporting = less taxes.
Stock Dating Standards
Stock dating is an important factor in stock rotation. The FDA doesn’t actually require expiration dates on food, except baby formula. The USDA has non-binding guidelines that suggest the use of “Best if Used By” language.
Due to the lack of uniform regulations, most states have implemented their own laws for dating with varying strictness. There is no broadly accepted industry standard for labeling among perishable foods, which leads to a lot of waste, mislabeling and consumer miseducation. Because of this, a lot of the language and usage for date labeling are added on the discretion of manufacturers and retailers.
Check out the interactive infographic below, which includes a sample from the 41 states that currently require some foods and perishables to have labels. A few have standards for all perishable goods, but most only cover goods such as milk, shellfish and eggs. Some are more clear, others are more ambiguous (*cough* Alabama).
The Grocery Manufacturers Association and the Food Marketing Institute are trying to change this. These two grocery industry leaders are spearheading an initiative to streamline product date labels in an effort to reduce waste and consumer confusion. They’re proposing the use of just two standard phrases: “BEST If Used By” and “USE By”, which follows the USDA’s suggested language.
“BEST If Used By” describes product quality, where the product may not taste or perform as expected but is safe to use or to consume.
“USE By” applies to the few products that are highly perishable and/or have a food safety concern over time; these products should be consumed by the date listed on the package-- and disposed of after that date.
BRAND TIP: if you’re going to change a product’s dating guidelines, you might as well run through the whole essential checklist for product labels to make sure there isn’t anything else you want to update.
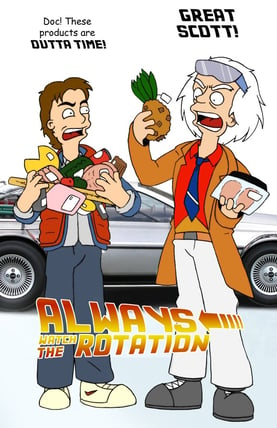
source
Stock Loss Mitigation
Even if a retailer has done the best it can to rotate stock and manage incoming product, sometimes expiration dates creep up anyway. Selling the product with a lower profit margin is better than a full loss plus the cost of disposal. In order to prevent the product from going bad on the shelf, retailers can put the product on sale and implement the following tactics to get it moving:
- Include the product in a printed daily or e-daily
- Sample the product to get more customers interested
- List the product on chalkboard easels and boards in front of and/or throughout the store
- Move the product to an end cap to get more traffic and eyes on the product
- Place the product on an attractive POP display
Stock rotation is a crucial component of stock management. Even if it isn’t directly under your job description, it is still important to be educated on what else goes on in product’s life from manufacturer to shopping cart. You’re ahead of the curve by taking the time to go through this stock rotation refresher. Keep it up. Now, go forth and rock your retail goals this week!